Patented and certified Bolt-Check system developed by R&D A/S offers accurate bolt tension measurements and traceability for wind turbines
Reduced repairs costs, increased reliability and support for long-term monitoring among key benefits of accurate tensioning; Correct bolt tension is hard to achieve but essential to safety and product reliability in farm equipment
Hinnerup, Denmark, 3rd May, 2021 – Measuring and maintaining the right tension of bolted joints to meet the exact needs of the wind turbine industry increases safety and reliability, and minimises the risk of failure and downtime. Applying these criteria, R&D A/S, a Danish engineering expert within the wind industry, developed the Bolt-Check solution that accurately measures bolt tension using ultrasonic sensors and software analysis. Recently approved by the challenging DNV-GL independent certification process for bolt clamping verification, the patented Bolt-Check solution can also digitally track individual bolts over their lifetime, which helps ensure that each bolt remains at its optimal tension.
Although essential to safety and product reliability, correct bolt tension is hard to achieve using the traditional torque and tension methods. And, as wind turbines continue to increase in size, it is more important than ever to maintain the integrity of the bolted joints in these structures, which need to withstand higher centrifugal and bending forces, as well as stresses and vibrations.
A wind turbine consists of thousands of different sized bolts holding structures together, often interdependently. Correct bolt tensioning is therefore critical, as one loose bolt can trigger a domino effect that, at worst, could result in the failure of the entire turbine.
No need to loosen bolt to check tension
The Bolt-Check system measures the length of the bolt as it lengthens in response to the application of load - torque or tension. These values are converted into accurate clamping force. During the bolt tensioning process at the assembly level, the operator observes the data live on the screen, and stops applying load once the desired tension has been achieved. Once in service, measurement of the bolt tension is possible without the need to loosen the bolts. This is because the system uses ultrasonic and mechanical length measurements as well as information about the material properties of the bolt batch. Combining these three values, makes it possible to measure and calculate the actual clamping force.
Accurate to within five percent, the Bolt-Check systems offers a superior advantage over traditional torque and tension methods, for which error tolerance can be as much as 30 percent. Compared to existing measurement solutions, Bolt-Check can be implemented at a fraction of the price and used directly on standard bolts.
“We noticed our engineers were often called to perform root cause analysis in relation to lose or broken bolts. We started analysing this issue and found out that the clamping load obtained by applied torque or tension often was found to be insufficient. So, we decided to find a solution for that and this is how Bolt-Check was developed,” says Søren Schmidt Kellenberger, Sales Director, Technology & Solutions, R&D A/S.
“The Bolt-Check system is not only highly accurate, it also has a competitive price tag compared to other sensor-based systems. The benefits to the wind turbine industry are wide-ranging and include reduced installation and maintenance costs and, of course, call-out charges and downtime costs, which can be significant, particularly in the offshore sector. Reduced risk of overall wind turbine failure ultimately offers peace of mind to wind turbine manufacturers,” adds Kellenberger.
Each bolt uniquely tagged
The Bolt-Check system can be used when installing new bolts and when evaluating existing bolts as part of determining the lifespan of wind turbines. As part of the full Bolt-Check system, a unique traceability-tag is added to each bolt, supporting pre-failure diagnosis and traceability, including the location of each bolt as well as its schedule of service and maintenance. No pre-treatment of the bolts is required.
DNV-GL product certificate
At the end of last year, the Bolt-Check system obtained DNV-GL product certificate allowing the Bolt-Check solution to be used for service and maintenance inspections as an alternative to torque or tension tools. The certificate provides independent verification that Bolt-Check fulfils the stringent standards of wind turbine tools and services. All DNV-GL type certification services are accredited by the German accreditation body DAkkS.
Bolt-Check, which is produced in Denmark and is supplied to wind turbine customers in several continents, is scheduled to be presented at the Husum Wind exhibition 14th-17th September 2021.
About R&D A/S
R&D A/S is an international engineering company that supplies knowledge, product development, and turnkey large-scale test systems for a range of industries.
What makes R&D A/S unique is our experience within all product development stages – from development and design to building test facilities and carrying out tests. We use our broad industry knowledge and highly specialized engineers to approach our customers' challenges from numerous angles to develop the right solution.
Our ambition is to supply individualized, sustainable, and innovative solutions that support our customers’ companies. That is how we create value through world-class engineering.
R&D A/S is a part of MTS Systems Corporation.
Media contact:
Dr. Malene Conlong
Tel: +49 171 699 2650 (Germany)
Email: M.conlong@mollerint.dk
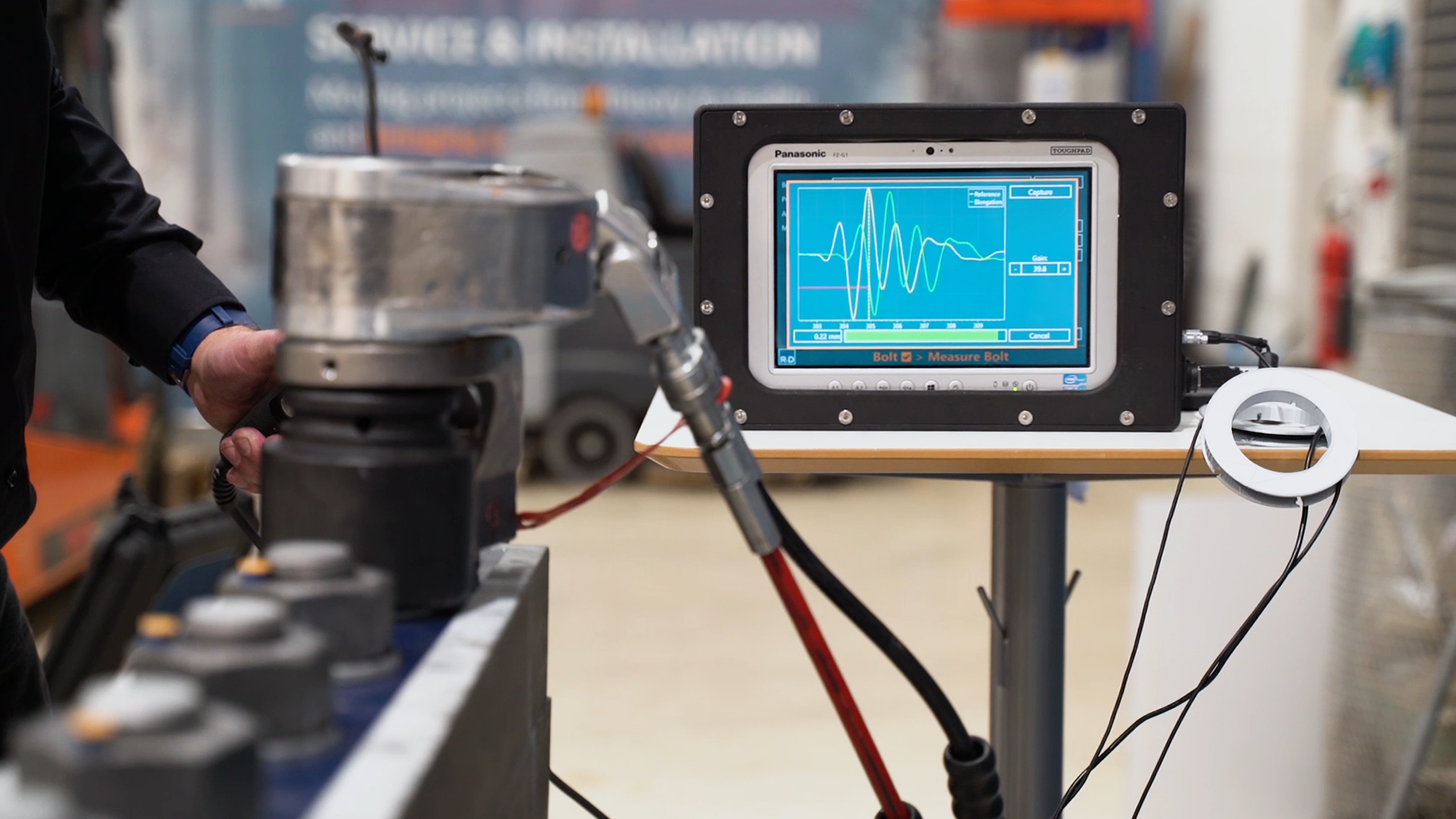
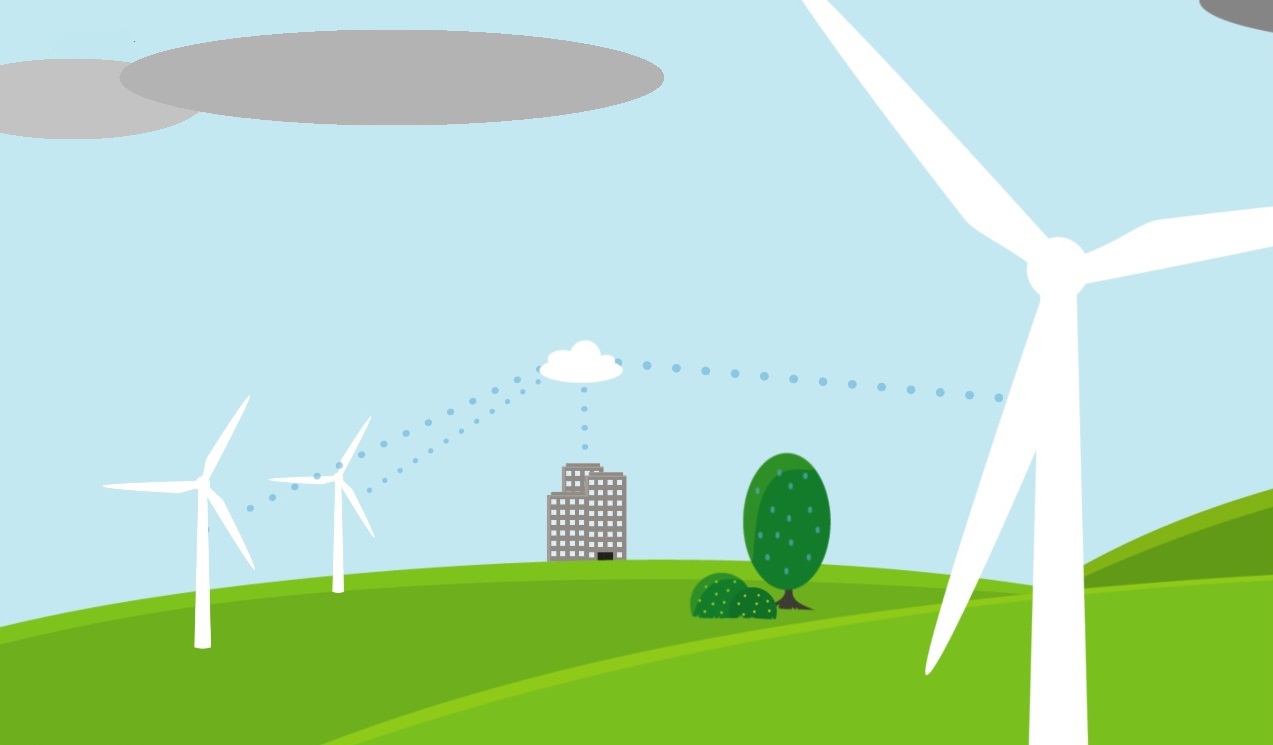